How to Reduce Bus Air Conditioning Maintenance Costs by 30%: A Fleet Manager’s Guide” ?
Bus AC maintenance costs, durable bus cooling systems, HVAC repair savings
Why Bus AC Maintenance Costs Are Spiraling Out of Control ?
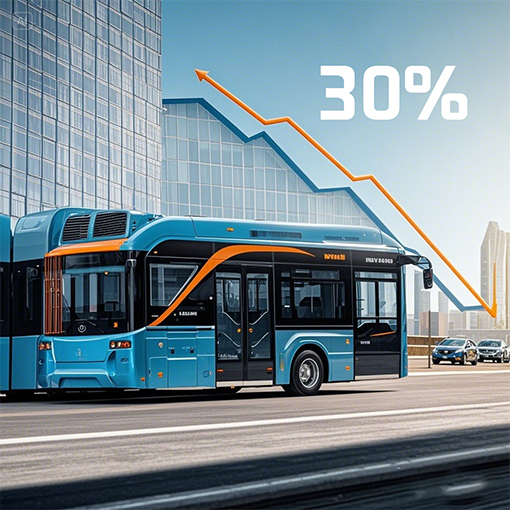
Commercial bus operators spend an average of $2,500–$4,000 annually per vehicle on air conditioning repairs, according to a 2023 industry report. Common culprits include:
– Clogged air filters reducing airflow and straining compressors.
– Refrigerant leaks from aging seals or corrosion.
– Electrical failures due to vibration-induced wire damage.
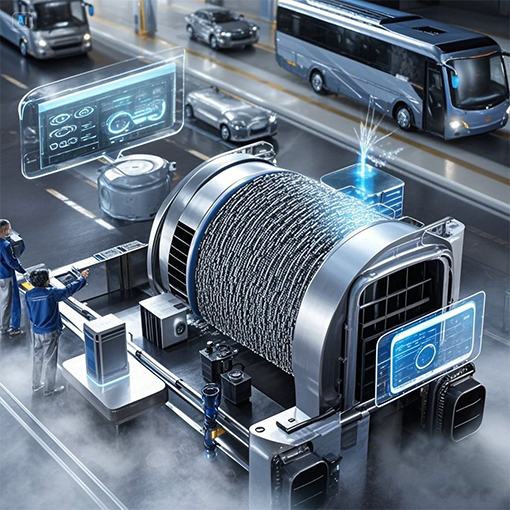
Proactive Strategies to Slash Maintenance Expenses
1. Invest in Self-Cleaning Filter Technology
Modern electrostatic filters capture 95% of dust particles and can be rinsed without disassembly. Brands like Caseter integrate these filters into their systems, reducing labor costs by 40%.
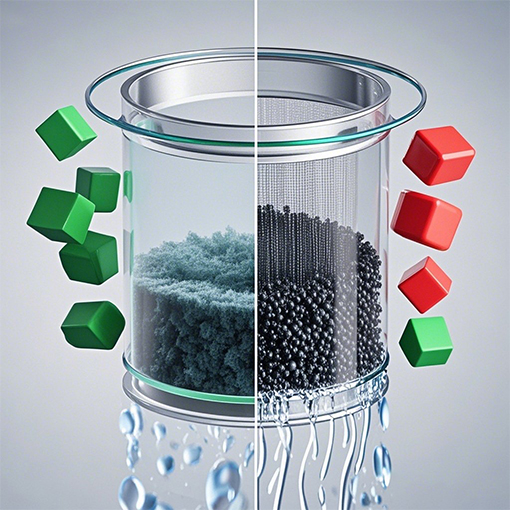
2. Adopt Predictive Maintenance with IoT Sensors
Real-time monitoring of:
– Refrigerant pressure (alert thresholds: <20 psi or >450 psi).
– Compressor temperature (ideal range: 50–80°C).
– Vibration levels (warning at >4.5 mm/s).
Example: A European fleet reduced unplanned downtime by 62% after installing Caseter’s SmartAC diagnostics.
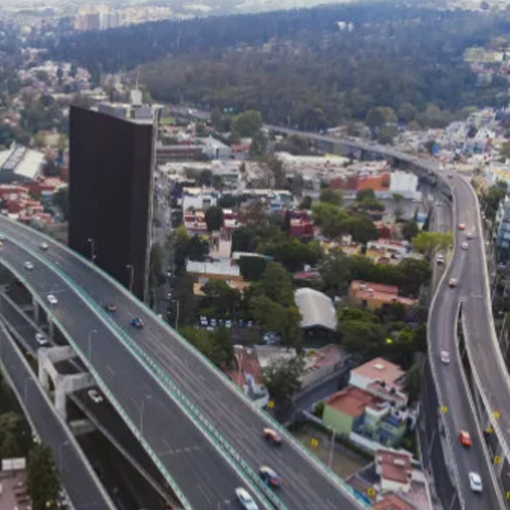
3. Upgrade to Corrosion-Resistant Components
Aluminum evaporator coils with hydrophilic coatings last 3× longer** than traditional copper tubes in coastal climates.
Case Study: Mexico City Transit Authority Cuts Costs
By switching to Caseter’s modular AC systems and implementing biannual professional servicing, they achieved:
– 28% reduction in annual HVAC repairs.
– 15% longer compressor lifespan.